Temper Mill vs. Stretcher Leveler (Cut to Length Lines)
Temper Mill cut to length lines and Stretcher Leveler cut to length lines have both been successfully utilized in applications where superior flatness and stability are required. Typically these applications include lasers, plasmas, or punch presses. When operated properly, both processes provide sheets/plates with minimal residual stress; however, the mechanisms to achieve this low residual stress state are different.
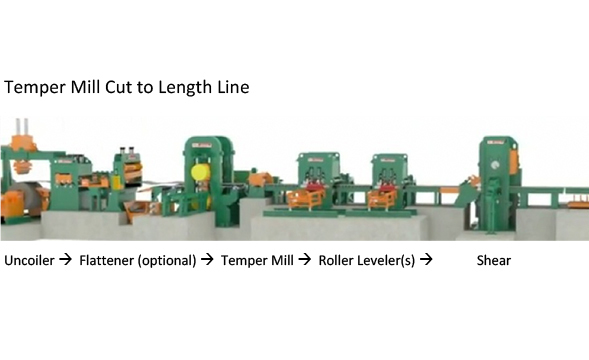
This article will discuss only one of the many Temper Mill uses; to improve shape in conjunction with a roller leveler on a cut to length line.
Temper mills work the sheet/plate material utilizing compression. The material thickness is compressed and elongated in the rolling direction. However, as temper mills do not have selective roll-bending across the strip width, a roller leveler must be used subsequent to the temper mill to create the final sheet/plate flatness and to correct for any remaining shape defects (coil set, edge wave, center buckle etc). Additionally, it is important that the incoming material “crown” profile (thicker center and thinner edges) match the temper mill roll profile, otherwise shape defects can be induced.
In applications where superior flatness and stability are required, temper mill cut lines have provided superior product to “roller leveler only” product and have been generally accepted as suitable for these applications. It is important to note that temper cut lines do not evenly exceed the yield strength of the material through the full thickness of the material (a gradient of multiple yield strains to zero exists from the surface to the centerline) and that the roller leveling that occurs after “tempering” actually introduces some residual stresses into the strip to create final sheet/plate flatness. Maximum shape correction is limited only by the % reduction capability of the temper mill (typically in the 2%-3% or 2000-3000 i-unit range); however, in practical application the specific order minimum gauge may limit the amount of correction allowed.
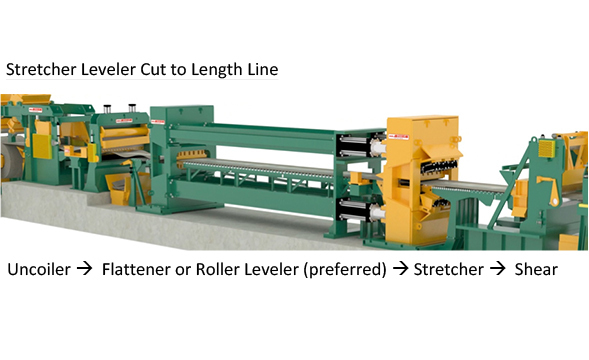
Stretcher Levelers
Modern stretcher levelers have gained acceptance in applications requiring minimal residual stress. In these applications, stretcher levelers have provided superior product to “roller leveler only” product and have been generally accepted as suitable for these applications.
Although some stretcher levelers have a flattener installed prior to stretching, it is beneficial to have a roller leveler installed prior to stretching in order to adequately remove crossbow (width-wise surface to surface length differential). This is important because the stretching portion of the process improves only length-wise shape defects (coil set, edge wave, center buckle, camber).
During the stretch cycle, the machine grips the steel and plastically deforms/stretches along the entire stretch length. This stretching is similar to the stretching associated with a tensile test. The plastic deformation is performed under tension vs the compression utilized by a temper mill. The yield strength of the steel is exceeded across the entire cross section of the material, which provides an “equalized” stress state in the sheet/plate. Additionally, the stress equalization process is the last process to occur prior to shearing so no further residual stresses are induced. One of the other benefits of stretcher leveling is that camber can be improved during the stretching process.
Maximum shape correction of a stretcher leveler is limited by two things. First, the width-wise shape correction (crossbow) is limited by the roller leveler horsepower and separating force. Second, the length-wise shape correction is limited by the % elongation maximum of the stretcher (hydraulic cylinder stroke ÷ stretch length, typically in the 2% or 2000 i-unit range). As with the temper mill above, in practical application the specific order minimum gauge may limit the amount of correction allowed.
“Temper Pass” Required
There are multiple reasons to specify temper passed material. In some cases the need for temper pass may be generic in nature and stretcher leveled product is comparable, while in some cases it is not. Table 1 below lists the typical end user reasons for specifying temper pass and if stretcher leveled product is an acceptable alternative.
Table 1: Typical End User reasons for specifying Temper Pass and if Stretcher Leveled Product is a comparable alternative.
Reason for Temper Pass Requirement (End User) |
Stretcher Leveled Acceptable? |
Notes |
Shape/Flatness |
Yes |
|
Minimal Residual Stress (Stability) |
Yes |
|
Coil Break Prevention |
Yes* |
*If the Stretch Leveler Line has the appropriate coil break prevention equipment |
Flatten Existing Coil Breaks |
No |
YPE is typically associated with fluting, orange peel, stretcher strain lines, luders bands, etc |
Remove Yield Point Elongation (YPE) |
Yes |
|
Table 2: Comparison of some of the benefits & limitations of the three main leveling technologies.
|
Roller Leveler Only |
Temper Mill/Leveler |
Leveler/Stretcher |
Shape Improvement Method |
Bending/Unbending (Alternating tension/compression) |
Mainly Compression via the temper mill |
Mainly Tension via the stretcher |
Capital Cost |
Low |
High |
Medium |
Operating Speed |
High |
High |
Medium |
Coil Set Improvement |
Yes |
Yes |
Yes |
Cross Bow Improvement |
Yes |
Yes |
Yes |
Edge Wave & Center Buckle Improvement |
Yes |
Yes |
Yes |
Surface Roughness Modification |
No |
Yes |
No |
Camber Improvement |
No |
Some |
Yes
|
Twist Improvement |
No |
Some |
Yes |
Flatness Potential |
< 5 i-Units |
< 5 i-Units |
< 5 i-Units |
Shape Improvement Potential |
< 200 i-Units |
2000 i-Units +1 |
2000 i-Units +1 |
Residual Stress (Stability) |
Low-Medium |
High (Better width-wise stability)
|
High (Better Length-Wise Stability)
|
1 The shape improvement potential of temper mills and stretcher levelers are line specific and dependent upon design capacities. These values are given as a reference relative to typical roller levelers for comparison purposes.
The link below is a May 2013 article from Modern Metals entitled “Upgrade to flat material”. It discusses stretch leveling vs temper mill cut to length lines from the viewpoint of a service center that operates both types of lines.
http://www.modernmetals.com/item/11517-upgrade-to-flat-material.html
by Rick Rowland